The TRINIDAT project is part of Clean Sky2 Fast Rotor Craft (CS2 FRC) and addresses the Next Generation Civil Tilt Rotor (NGCTR) configuration. The TRINIDAT project started at 1 February 2019 and ended at 30 April 2022.
The NGCTR configuration is being developed by Leonardo Helicopters. The main benefit of the NGCTR configuration is that it offers reduced travel time on short and medium distances up to 500 nautical miles (approx. 1000 km), as shown in the figures below.
The engine intake has a rather complex shape due to the tilting rotor head concept of the NGCTR configuration. The intake duct changes from an elliptical cross-section to an annular cross-section of the Air Intake Plane (AIP) for the engine, as shown in the picture below.
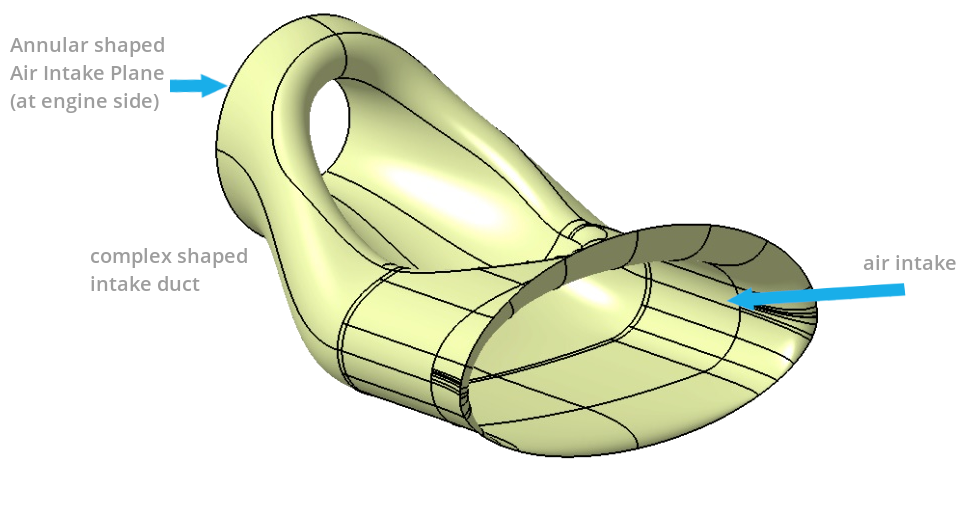
The TRINIDAT project addresses the aerodynamic characterization of the intake geometry (as supplied by Leonardo Helicopters) and optimization of the intake duct geometry (within certain given geometric constraints) by using CFD (Computational Fluid Dynamics) based optimization tools. The objective of the optimization study is to improve the flow steadiness and uniformity at the Air Intake Plane of the engines such as to comply with the requirements put forward by the engine manufacturer. The initial characterization and optimization will rely on dedicated CFD studies. The final validation will be made with full size model tests in the DNW-LLF 6×6 wind tunnel, allowing reliable testing at full scale Mach and Reynolds conditions. A sketch of the model in the wind tunnel is shown below.
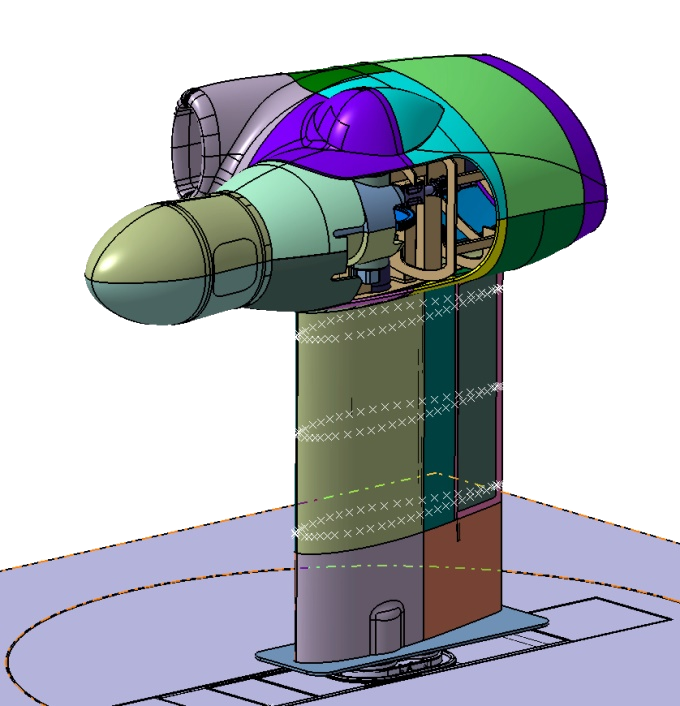
For efficient testing of basic and optimized intake geometries in airplane, helicopter and intermediate Extreme Short Take-Off and Landing mode, a modular wind tunnel model equipped with a remotely controlled tilting rotor hub will be designed and manufactured. In order to characterize the flow in the intake ducts these will be equipped with approx. 400 static pressure ports. In order to characterize the flow over the outboard wing approx. 200 additional static pressure ports will be installed. A remotely controlled highly instrumented rotatable rake will be installed to enable detailed and efficient measurement of the flow at the engine air intake plane. This rake will be equipped with 8 total pressure rakes, each having 5 total pressure sensors. Two of these rakes will have combined steady and unsteady total pressure sensors. Two additional rakes will be equipped with five 5-hole probes in order to measure flow swirl velocities in the air intake plane. Finally, the wind tunnel model will be equipped with a remotely controlled aileron. The use of remote controls enables an efficient measurement campaign.
Apart from the aerodynamic optimization of the intake and its testing, the project will also identify icing and snow conditions to be considered for certification and will subsequently analyze the ice and snow effects on the nacelle inlets and ducts to provide early input for anti-icing measures that might be needed for the NGCTR.
Results
In September 2020, a wind tunnel test campaign with the basic intake configuration has been performed successfully. A clarifying announcement can be found on the website of Clean Sky, see Innovative design for tilt rotor nacelle and intake duct breezes through wind tunnel test | Clean Sky
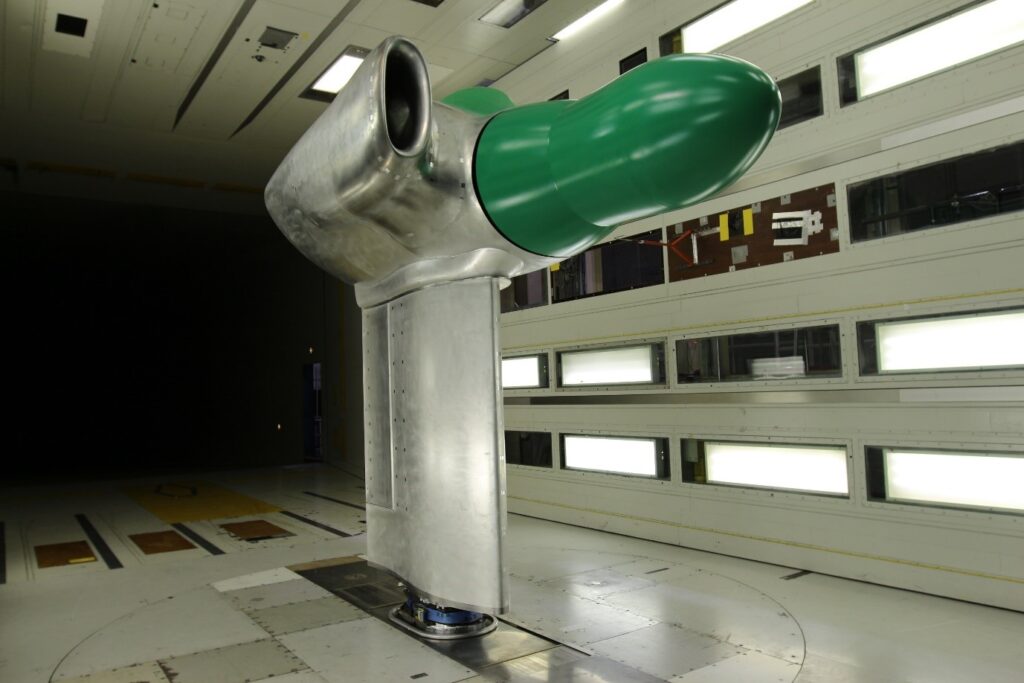
In order to define the optimized intake geometry, extensive numerical investigations are conducted. These simulations involve various design routes like Adjoint-based Design Optimization, Adjoint-based Inverse Design and Geometry Parametric variation. Several geometry constraints should be taken into account, such as rotor hub shaft, aft AIP region and hydraulical region. In addition, several constraints for the flow quality (distortion parameters) should be respected. The following figures illustrate the optimized intake time-averaged flow solution (total pressure in AIP, identical contour ranges) as defined for the model design and manufacturing phase.
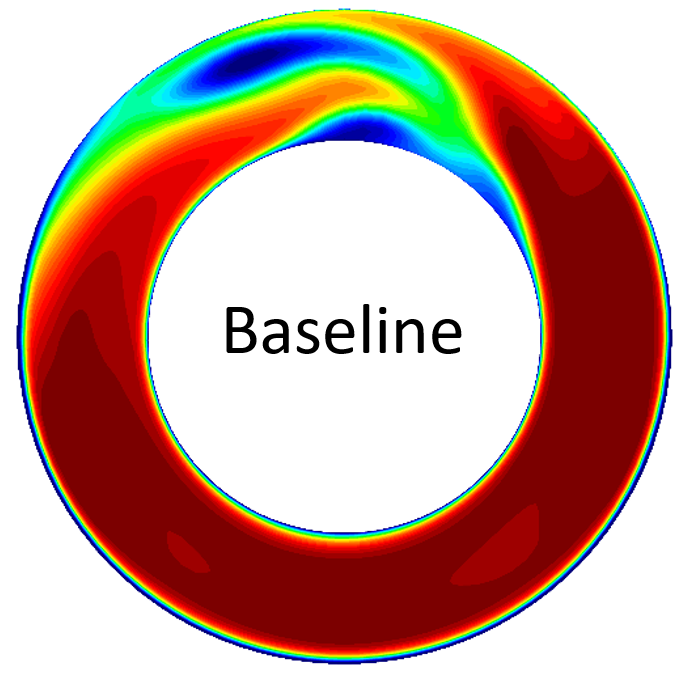
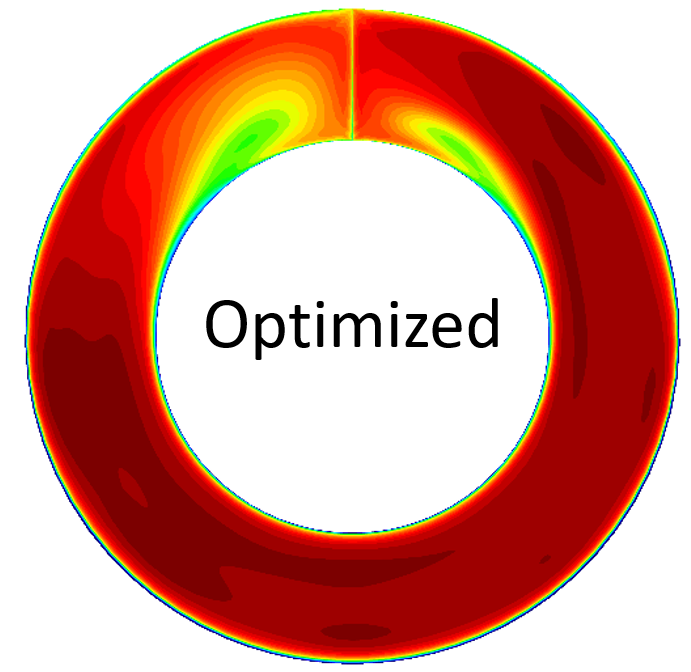
In July 2021, the second wind tunnel test campaign including the optimized intake configuration has been performed successfully. Overall, experimental and numerical investigations within the TRINIDAT project both revealed that the optimized intake shows significant improvement of the flow quality at the AIP.
Dissemination
During the TRINIDAT project early results have been presented at the 47th European Rotorcraft Forum in 2021. These and future publications will be made public on an Open-Access data repository, meeting H2020 requirements. The link will become available on this website soon. A selected set of numerical and experimental results as open access data will become available as well.
Paper 1
Paper 2
Paper 3
Partners and Topic leader
A total of six partners are collaborating in the TRINIDAT project in order to comply with the project requirements of Topic Leader Leonardo Helicopters. The role of the different partners is summarized below:
Contact
For further information about the TRINIDAT project please contact:
Dr.ir. Remco Habing
Department Helicopters and Aeroacoustics
Netherlands Aerospace Centre NLR
Voorsterweg 31
8316 PR Marknesse
The Netherlands
Email: remco.habing@nlr.nl
Phone: +31 88 511 4418