A clear step beyond state of the art 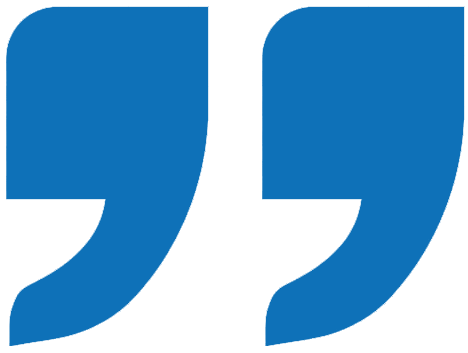
The objectives
Thermoplastics materials are more ductile than thermosets and are therefore more robust with respect to impact damage. Advanced welding techniques allow a high level of parts integration, eliminating to a large extent the application of costly fasteners, commonly used in traditional thermoset composite parts. Also hot forming processes allow more out of autoclave operations, which results in dramatically more energy-efficient production when with thermoset materials. In economic terms, these technical advantages enable an approximately 10% lower production cost level and 5-10% reduction in maintenance cost.
To develop and manufacture the tail section for the NGCTR, achieving the maximum weight benefits possible for the current state of the art through the application of new thermoplastic materials. LIFTT is aiming for 20% weight benefit for a series production design when compared to aluminium and 5-10% when compared to thermoset composites.
To develop a new design and industrialization methodology, reducing lead time (T), cost (C) and risk (R) in the design phase by at least 50%. In the design steps, changes can be more easily included and reviewed on cost, weight and associated risk before adopted in final design, where KBE tools support the design- and analysis processes.
LIFTT highlights
Activities, induction welding of:
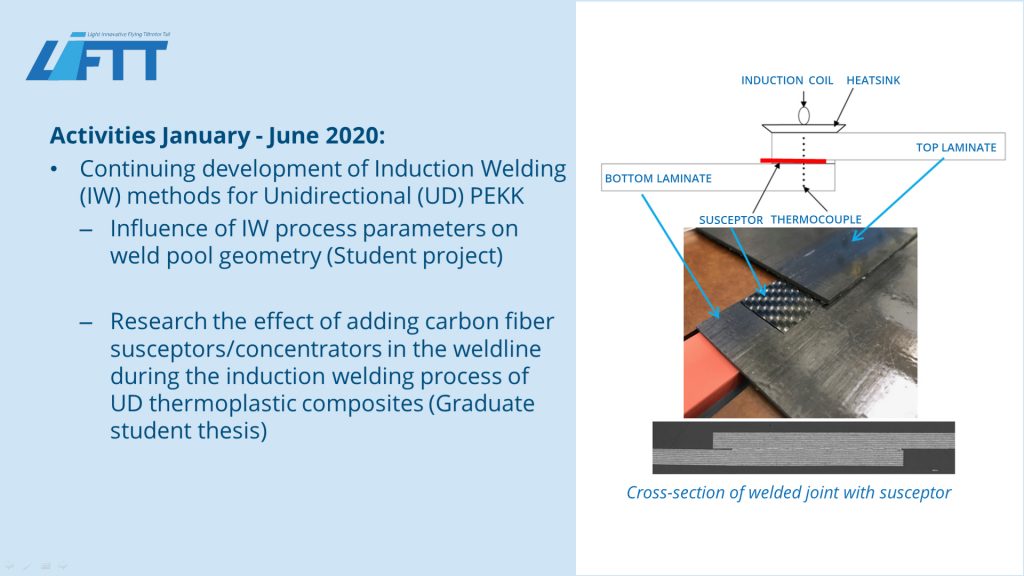
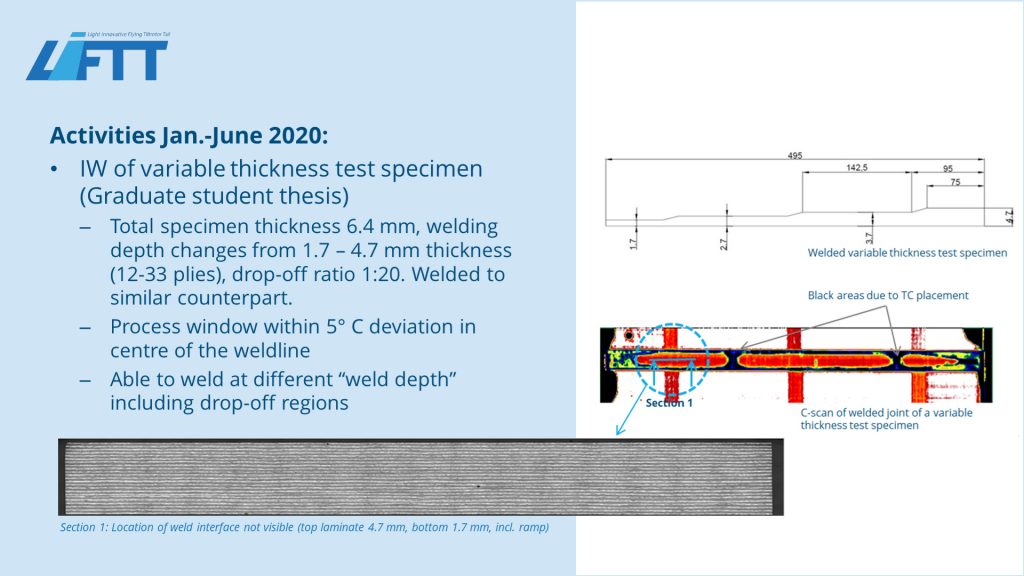
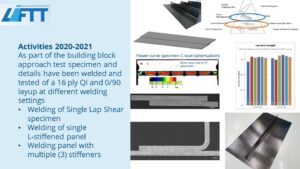
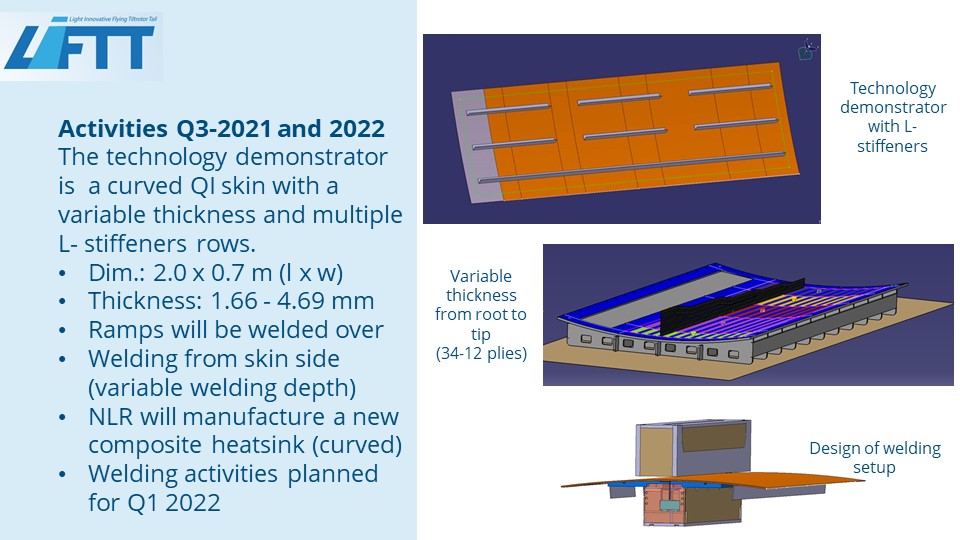
Demonstrator Development: Preliminary Design Phase
The LIFTT project started officially in March 2018, with a Kick-Off meeting with the project partners in Cascina Costa at the facilities of Leonardo Helicopters. During the Kick-Off meeting we discussed the objectives, scope and time schedule of the project. A few weeks later, the LIFTT team received a requirements list, which was used as basis for the discussions during the requirements review, held in August 2018. In between, the LIFTT team and Leonardo Helicopters organized several technical workshops to work together on the initial concept of the V-Tail, required to enter the PDR phase.
After the requirements review, the LIFTT team entered the PDR entry phase. Leonardo Helicopters supplied the entry and exit requirements of the PDR phase and the LIFTT team matured the concept accordingly. This resulted in the successful closure of the PDR phase in February 2019.
Demonstrator Development update: PDR and CDR
Due to weight issues of the NGCTR-TD aircraft, the design concept of the V-Tail was changed in order to reduce weight to meet Leonardo weight campaign goals and to avoid heavy limitations on the flight envelope. The concept change should further reduce structural weight, but it also excludes one of the key technologies of the project.
The concept change contains the replacement of the thermoplastic fixed fin skins with thermoset sandwich skins. In addition, the ruddervator concept is changed from a metal multi-rib version to a full depth sandwich ruddervator. Due to LIFTT consortium budget and schedule restrictions, Leonardo helicopters agreed to design and manufacture the honeycomb parts and LIFTT will remain responsible for design and manufacturing of the remaining parts.
Due to this major concept change the tail concept was pushed back into the preliminary design phase. A second preliminary design review was held in October 2020, where the new concept was successfully reviewed. After closing the PDR, the concept design entered the Critical Design phase. Due to several major issues, the expected finish of the CDR phase is beginning of quarter 4 of 2021.
After this phase, the project will enter the demonstrator manufacturing phase. In parallel, project partner RAMAL already started the design of the tooling for parts production and assembly. CFP partners VZLU and A-RC are designing and developing a full-scale test rig to test the fixed fin with new thermoplastic technologies under realistic conditions. In parallel, fundamental research is executed to support technology development for future thermoplastic applications through testing of samples and a panel.
Technology Development: Thermoplastic composites
Within LIFTT, several thermoplastic composites technologies are considered. Some of them will be implemented into the flying tail demonstrator and a few will be developed for implementation beyond this project.
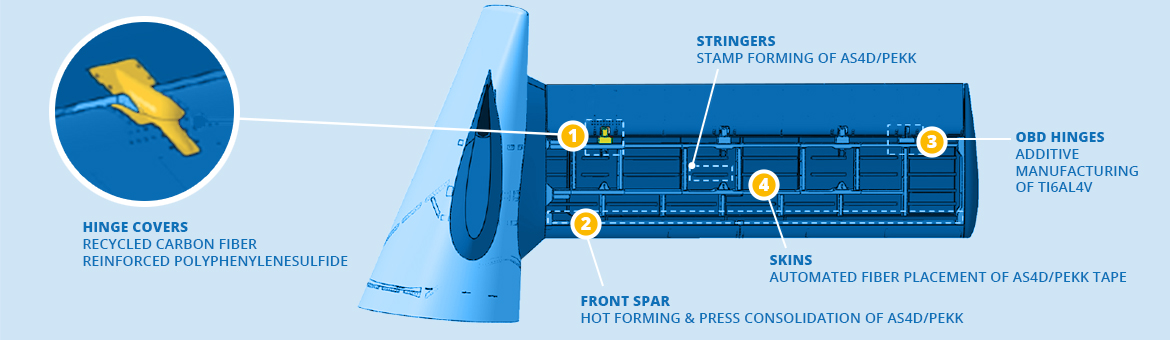

Recycled carbon fiber reinforced thermoplastic hinge covers (flying)
The recycling process consists of several steps. Carbon fibre reinforced polyphenylene sulfide waste material is collected and shredded to flakes with a long fibre length.
The material is heated and mixed in a low-shear mixer and compression moulded to a part. This solution offers the possibility to process long fibre lengths, known to exhibit high modulus, strength and impact properties.

Out-Of-Autoclave press consolidated thermoplastic front spar (flying)
The Hot Forming & Press Consolidation development of AS4D/PEKK supports the production of complex and integrated small to mid-size carbon fibre parts for aerospace applications.
Its intention is to enclose the gap between the benefits of stamp forming (low curing time, high rate, low labour) combined with the larger scale and complex parts which are currently manufactured with an autoclave cycle.

Additive manufactured hinge (not flying)
Currently AM technology has found its first applications in aircraft at non-flight critical parts, mostly applying
well known machining constraints to the shape of the component. In this case, standard calculation methods can be used for substantiation. Next step is to develop a design process supporting the application of flight
critical parts with optimized shapes. By investigating the outer boundaries of the AM technology including
topology optimization and testing (with emphasis on fatigue life) the results, the intention is to derive design principles and calculation methods for robust lightweight design solutions.

Skins
Due to weight issues of the NGCTR-TD aircraft, the design concept of the V-Tail was changed in order to reduce weight to meet Leonardo weight campaign goals and to avoid heavy limitations on the flight envelope. The concept change however excluded one of the key technologies of the project. The thermoplastic fixed stiffened fin skins originally intended are replaced with thermoset sandwich skins. In addition, also the ruddervator concept is changed from a metal multi-rib version to a full depth sandwich ruddervator.
Technology development: Thermoplastic composites update
Recycled Carbon Fiber Reinforced Thermoplastic hinge covers (flying)
Six hinge covers in total will be installed: three on the left tail plane and three on the right tail plane. A hinge cover consists of two parts. One part will be installed on the fixed fin skins and one part on the ruddervator skins. As the name already suggests, the hinge covers are placed over the hinges, which are located aft from the actuators.
The design of the hinge covers have been frozen in May 2021. Immediately, the development of tooling for production was started. In a very short time, the tooling was ready and the first batch of hinge covers were produced. The first produced parts show already good quality and will be used for application on the flying tail.
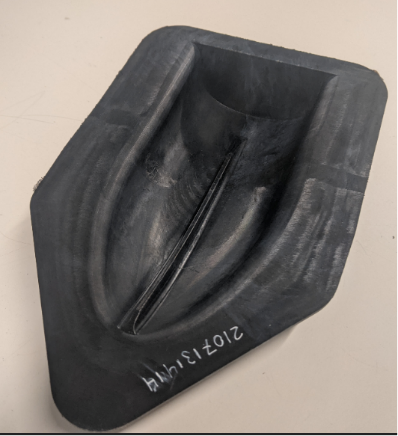
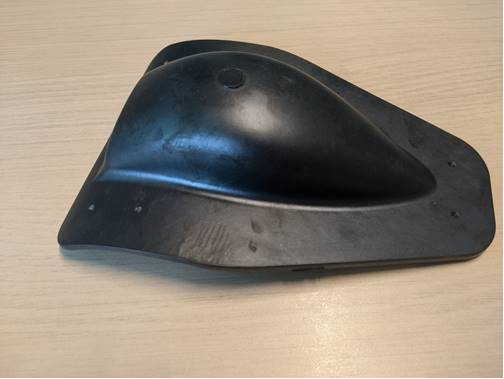
Out-Of-Autoclave press consolidated thermoplastic front spar (flying)
It was decided to divide the development of the front spar in a stepping stone approach. For TRL4, it means that first a half-meter spar was produced with a step and a joggle, taken from the full-scale spar. All process evaluations show that the process is robust and the product quality is comparable with in-autoclave products. The TRL4 level was successfully achieved end of June 2021. The next challenge is to produce a full-scale spar of 3.2 meter length with all the necessary features, such as steps and joggles. Again, the quality needs to be at least similar to an in-autoclave product. Qualification activities should prove this, to support the Permit-to-Fly for the aircraft. It is expected that TRL5 will be reached end of quarter 1 in 2022. This includes the production of the front spars for assembly in the flying demonstrator.
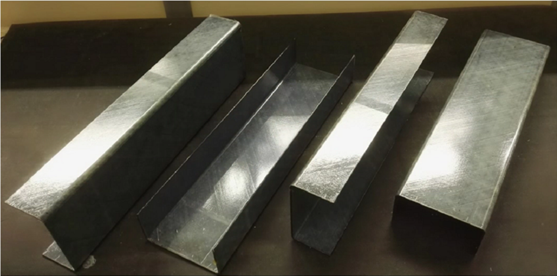
Dissemination
During the SAMPE Europe Conference 2021 Baden/Zürich – Switzerland a paper was presented called; Technology development towards induction welding of a UD-PEKK tail section with stiffeners by Senne Sterk. The paper detailing the technology development regarding Induction Welding can be downloaded here.
Project timeline
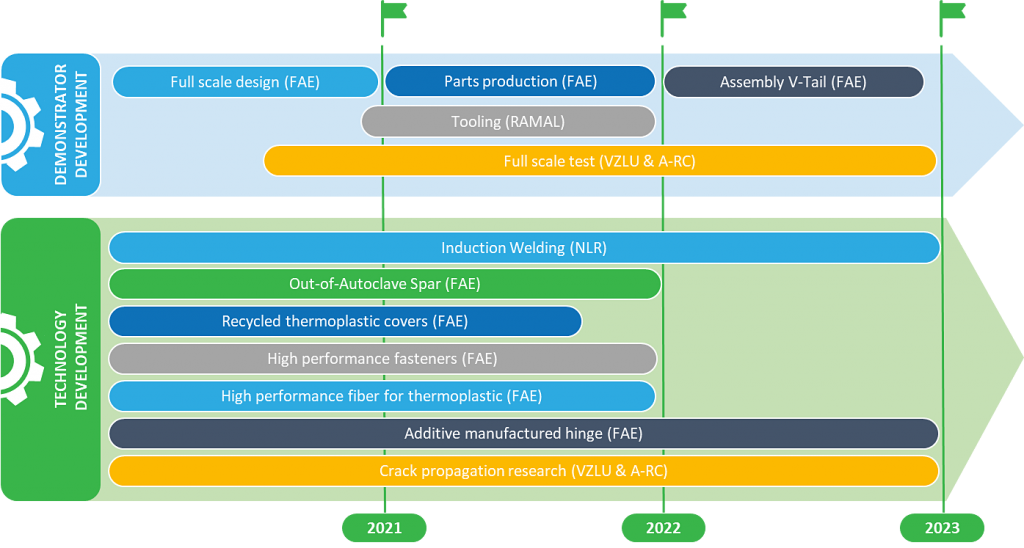
LIFTT partners
NLR – Royal Netherlands Aerospace Centre
P.O. Box 90502
1006 BM Amsterdam
The Netherlands
www.nlr.org